The Revolutionary Impact of Laser Sintering Technology on Modern Business
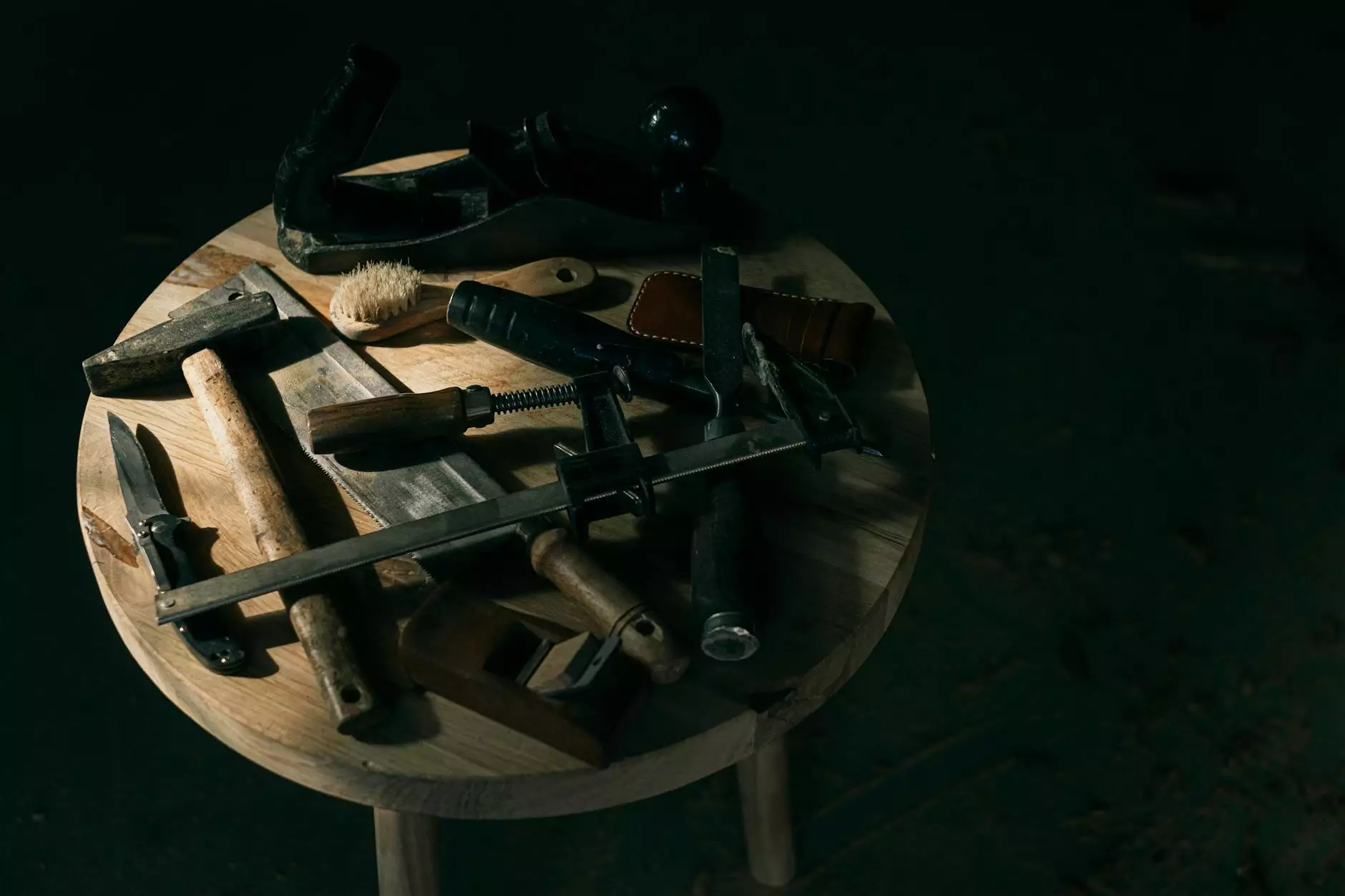
The world of business is continuously evolving, fueled by advancements in technology that redefine how products are designed, manufactured, and marketed. One of the most transformative innovations in recent years is laser sintering technology, a method that is proving to be a game changer across multiple industries, including art supplies, product design, and 3D printing.
Understanding Laser Sintering Technology
Laser sintering technology, often referred to as Selective Laser Sintering (SLS), is an additive manufacturing process that uses a laser to fuse powdered materials into solid structures. This innovative technique allows for the creation of complex geometries and intricate designs that are often impossible to achieve with traditional manufacturing methods.
The process begins with a digital 3D model, which is sliced into layers by specialized software. The powder material is then spread in a thin layer across the build platform, and a laser beam selectively melts the powder according to the 3D design. After each layer is completed, the platform lowers to allow for the application of the next layer of powder, continuing until the part is fully formed.
The Advantages of Laser Sintering Technology
There are numerous advantages to incorporating laser sintering technology into business operations:
- Design Flexibility: SLS allows designers to create intricate and complex shapes that traditional methods simply cannot achieve.
- Material Efficiency: This technology minimizes waste by using only the necessary material to produce a part, making it an environmentally friendly option.
- Rapid Prototyping: Businesses can develop prototypes quickly, allowing for faster iteration and reduced time-to-market.
- Customization: SLS enables the production of customized items tailored to specific customer needs, enhancing user satisfaction.
- Durability and Strength: Parts produced via laser sintering are often stronger and more resilient than those made with traditional manufacturing techniques, thanks to the uniform density achieved in the process.
Impact on Art Supplies
In the realm of art supplies, laser sintering technology is revolutionizing how artists and designers create and experiment with tangible art forms. Artists can utilize the technology to produce unique sculptural pieces, allowing for greater expression and innovation.
For example, the use of SLS in creating custom paintbrushes, unique tools, or even complex art installations provides artists with unprecedented opportunities. They can produce items tailored to their exact specifications and styles, thus enhancing their creative process.
Transforming Product Design
In product design, laser sintering technology is changing the landscape by streamlining the development process. Designers are now able to create high-fidelity prototypes quickly and efficiently.
Rapid Development Cycles
The fast turnaround time associated with SLS means that designers can test multiple iterations of a product quickly. This rapid development cycle allows for:
- Iterative Testing: Identifying design flaws and making necessary adjustments before moving into mass production.
- Cost-Effective Trials: Reducing costs associated with traditional prototyping materials and processes.
Enhancing Collaboration
Furthermore, laser sintering technology facilitates better collaboration among stakeholders. Designers can produce tangible prototypes for presentations, making it easier to communicate ideas and gain feedback from clients or team members. These prototypes can significantly influence decision-making and enhance the design process.
Advancing 3D Printing
3D printing, also known as additive manufacturing, has benefitted immensely from the implementation of laser sintering technology. The ability to create complex parts from a range of materials has opened doors to unimagined possibilities in manufacturing and production.
Material Versatility
Unlike traditional 3D printing methods that are limited to plastics and resins, SLS can utilize a variety of materials, including but not limited to:
- Polyamide: Known for its strength and durability, perfect for functional prototypes.
- Metals: Used in engineering applications where strength and thermal resistance are critical.
- Composite Materials: Combining plastics with other materials for enhanced performance.
Industrial Applications
The industrial applications of 3D printing using laser sintering technology are vast. Industries ranging from aerospace to automotive are leveraging SLS for producing end-use parts. For instance:
- Aircraft components that are lightweight yet robust.
- Custom tools for manufacturing processes that increase efficiency.
The Future of Laser Sintering Technology
As technology continues to evolve, the future of laser sintering technology appears incredibly promising. Continuous advancements in software and materials are leading to even better printing resolutions and capabilities.
Integration with AI and Automation
The integration of artificial intelligence and automated processes into SLS could lead to:
- Improved Quality Control: Utilizing AI to monitor the printing process and adjust parameters in real-time to ensure the highest quality output.
- Reduced Lead Times: Automating material handling and post-processing tasks to further streamline production.
Sustainability Considerations
Furthermore, sustainability will continue to be a key driver for the adoption of laser sintering technology. As businesses aim to reduce their environmental footprint, the efficient use of materials and energy associated with SLS makes it an attractive option.
Conclusion
In conclusion, the transformative power of laser sintering technology is reshaping the landscape of modern business. From enabling artists to express creativity more freely in art supplies, to revolutionizing product design and advancing the field of 3D printing, the applications of this innovative technology are both diverse and profound.
As businesses embrace these advancements, they unlock new levels of efficiency, creativity, and profitability, paving the way for a future where laser sintering technology plays a pivotal role in shaping industries worldwide.